Understanding O Ring Face Fitting: A Comprehensive Guide
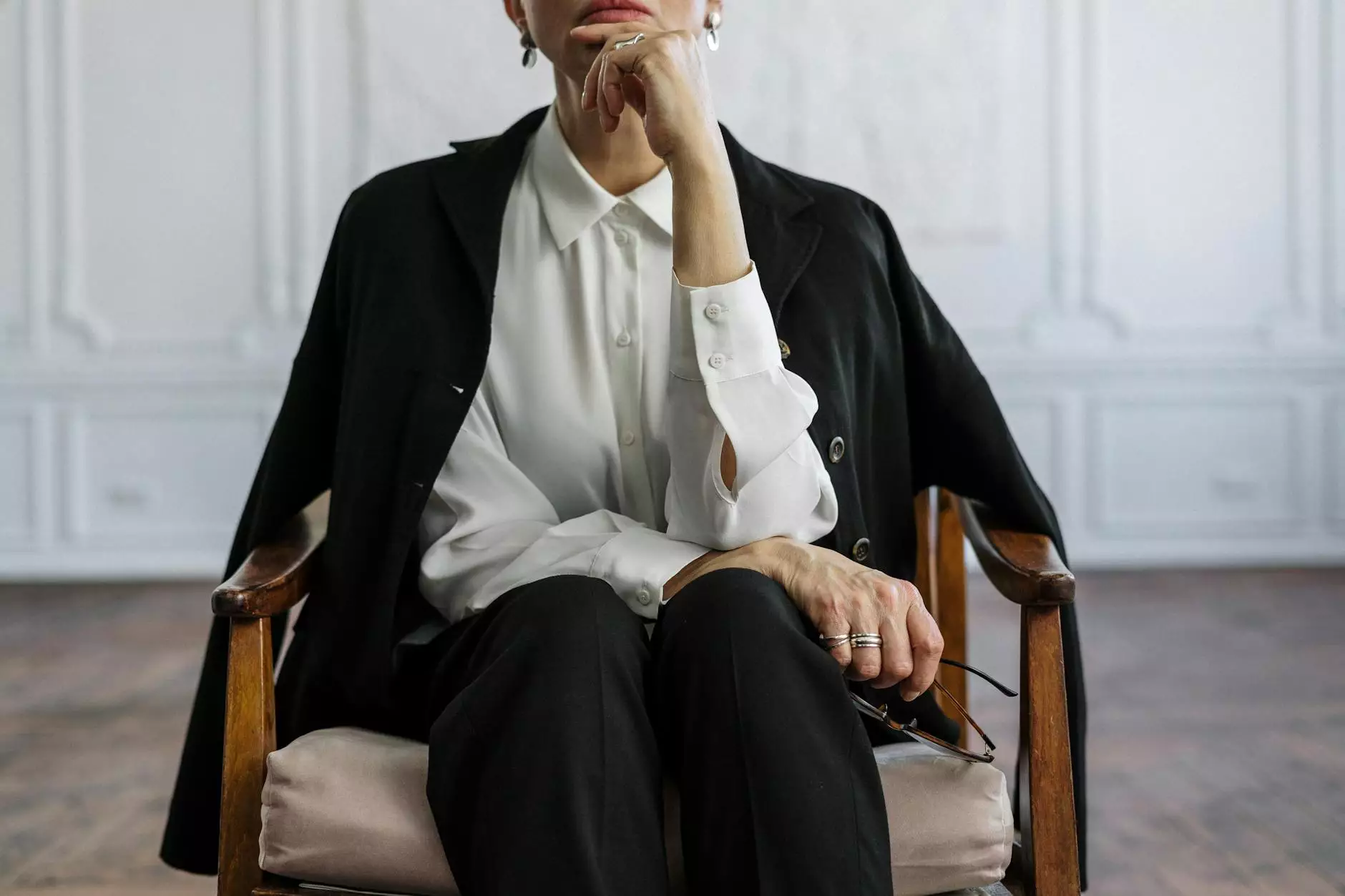
In the realm of industrial fittings, the term O ring face fitting frequently comes up due to its unmatched efficiency and reliability in various applications. This article will delve into the definition, advantages, applications, and manufacturing of O ring face fittings. By the end, you will have a profound understanding of why these fittings are critical for operations across multiple sectors.
What is an O Ring Face Fitting?
An O ring face fitting is a type of connection used to join two components in a fluid transfer system. It typically consists of a facepiece with a groove for an O ring, which acts as a seal. When the connection is made, the O ring is compressed, creating a tight seal that prevents leakage of fluids or gases. This makes it essential for applications requiring pressure retention and fluid containment.
Benefits of O Ring Face Fittings
O ring face fittings offer numerous advantages, making them a popular choice in various industries, including:
- Leak Prevention: The primary benefit of O ring face fittings is their ability to prevent leaks. The O ring compresses during assembly, creating a hermetic seal that minimizes the potential for fluid escape.
- Durability: Designed to withstand extreme conditions, O rings are made from various materials that can resist heat, chemicals, and physical wear, ensuring a long-lasting connection.
- Ease of Installation: The design of O ring face fittings allows for easy installation and removal, which is advantageous in systems where frequent maintenance is required.
- Versatility: O ring face fittings can be used with a range of fluids and gases, making them suitable for applications in hydraulics, pneumatics, and other sectors.
Applications of O Ring Face Fittings
The applications for O ring face fittings span various industries, demonstrating their versatility and reliability:
1. Hydraulic Systems
In hydraulic systems, O ring face fittings are crucial for connecting hydraulic hoses and components effectively. They help maintain pressure while preventing fluid leakage, which is essential for optimal performance.
2. Pneumatic Systems
Similar to hydraulic systems, pneumatic systems rely on O ring face fittings to ensure airtight connections are made between air hoses and machinery, facilitating efficient energy transfer.
3. Oil and Gas Industry
Due to their ability to withstand harsh environments, O ring face fittings are widely used in oil and gas applications, where they protect against leaks that could result in catastrophic failures.
4. Chemical Processing
In chemical processing, using O ring face fittings helps ensure the safe transit of corrosive and hazardous materials, as they can be manufactured with materials resistant to a wide range of chemicals.
5. Food and Beverage Industry
In the food and beverage industry, hygienic applications are paramount. O ring face fittings can be made from food-grade materials, ensuring compliance with health and safety regulations.
Key Considerations When Choosing O Ring Face Fittings
When selecting O ring face fittings for your application, consider the following factors:
- Material: Choose O rings made from materials compatible with the fluids they will come into contact with, considering factors such as temperature, pressure, and chemical exposure.
- Size: Ensure that you select the correct size of O ring face fitting to ensure a secure and effective seal.
- Pressure Rating: Verify that the fittings can handle the pressure levels in your system to avoid catastrophic failures.
Manufacturing of O Ring Face Fittings
The manufacturing process of O ring face fittings involves several key steps:
1. Design Specifications
It begins with defining the appropriate design specifications based on the intended application. CAD software is often employed to accurately design the fittings according to specific requirements.
2. Material Selection
Next, manufacturers select the materials based on the application's needs. For example, O rings may be made from rubber, silicone, or fluoropolymers, depending on the requirements for temperature and chemical resistance.
3. Production
Once the designs and materials are ready, the production of fittings occurs. This may involve processes such as molding, machining, and assembly to ensure precision and accuracy.
4. Quality Control
After production, fittings undergo rigorous quality control checks. This ensures that they meet industry standards and specifications for performance, safety, and durability.
Conclusion
In conclusion, O ring face fittings are essential components for ensuring secure and leak-free connections in various industries. Their versatility, durability, and safety make them invaluable in applications where fluid containment is critical. At fitsch.cn, we offer a wide range of high-quality fittings to meet your specific needs. Understanding the importance of O ring face fittings and their applications will help you make informed decisions when sourcing fittings for your business.
Explore Our Offerings
To see our extensive range of fittings for sale, please visit our website at fitsch.cn. Here, you can explore our collection, read more about our products, and understand how our offerings can benefit your operations. We are committed to providing top-notch fittings that guarantee reliability and efficiency in your projects.