Automotive Injection Molding: Revolutionizing the Auto Industry
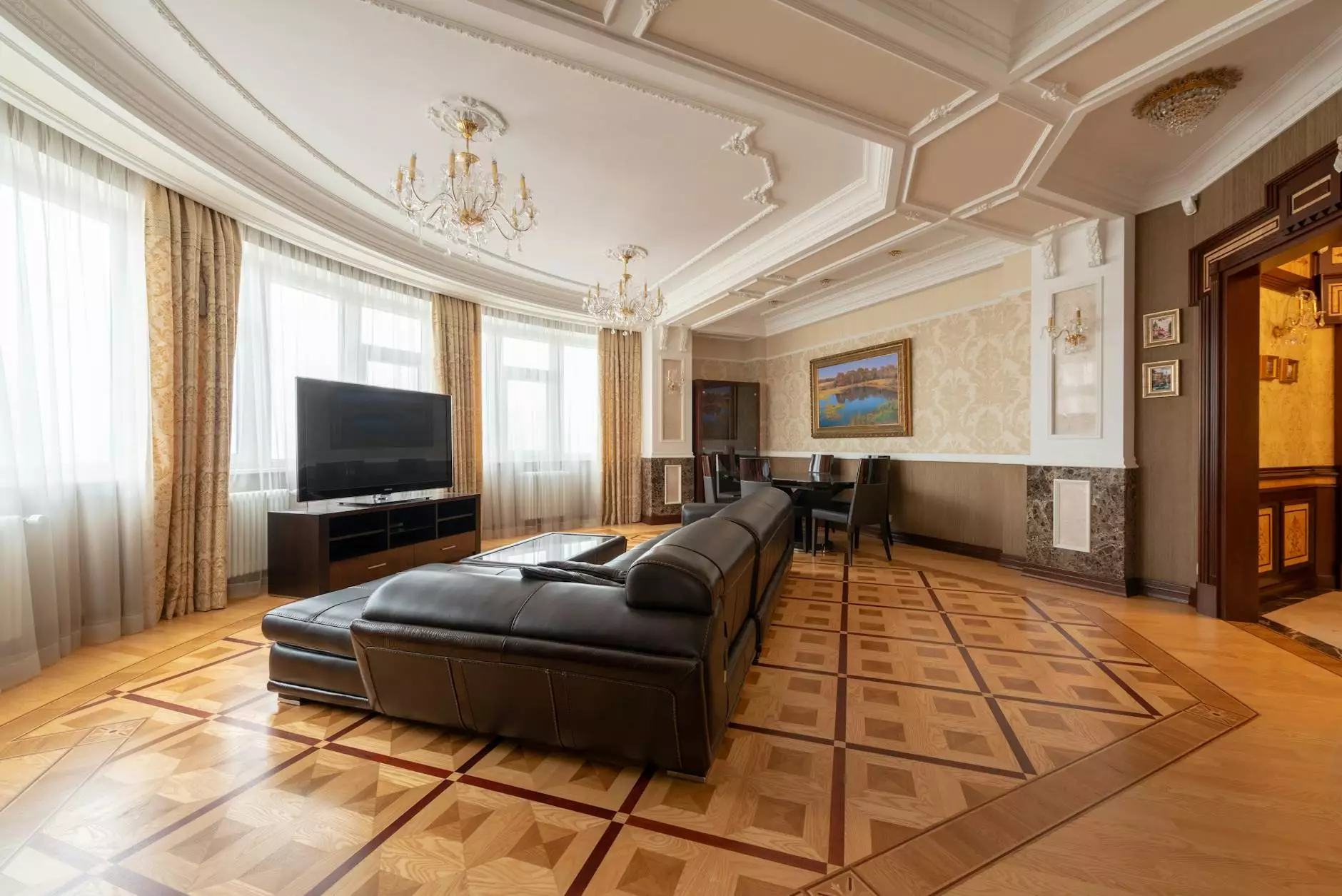
Automotive injection molding is a pivotal process in the modern manufacturing landscape. It involves the production of intricate plastic components that are vital for automotive assembly. This article delves into the numerous advantages, applications, and innovations surrounding automotive injection molding that are shaping the future of the automotive industry.
The Importance of Automotive Injection Molding
In today's fast-paced automotive industry, manufacturers seek methods to enhance efficiency and reduce costs while maintaining high standards of quality. Automotive injection molding serves this purpose exceptionally well. It not only streamlines production processes but also offers unparalleled design flexibility, allowing engineers to create components that are lightweight yet robust.
Cost-Effectiveness and Efficiency
One of the most compelling reasons for the widespread adoption of automotive injection molding is its cost-effectiveness. The initial setup cost may be significant, but once the molds are created, the per-unit cost drops dramatically. This is particularly beneficial in the automotive sector, where large quantities of parts are required.
- High Production Rates: Injection molding allows for rapid manufacturing, producing thousands of units in a short timeframe.
- Material Efficiency: Minimal waste is produced during the molding process, making it an environmentally friendly choice.
- Automated Production: Automation technologies can be applied, further enhancing production speed and reducing labor costs.
Design Flexibility
The versatile nature of automotive injection molding provides designers with the freedom to innovate. Complex geometries that were once deemed challenging to manufacture can now be easily produced.
- Intricate Details: Fine details and textures can be incorporated seamlessly into the design.
- Multi-material Capabilities: Different materials can be molded together in a single component, enhancing functionality and aesthetics.
- Streamlined Assembly: Parts can be designed to snap together, reducing the need for additional fasteners and saving time on assembly lines.
Applications of Automotive Injection Molding
The applications of automotive injection molding are as diverse as the automotive industry itself. Below, we explore some of the key areas where this technology is making a significant impact.
Interior Components
The interior of a vehicle is not only about comfort but also about aesthetic appeal. Injection-molded components such as dashboards, center consoles, and door panels play crucial roles. Here’s how injection molding enhances interior components:
- Durability: Materials used in injection molding are often resistant to wear and tear, ensuring longevity.
- Aesthetic Customization: Various finishes and colors can be applied, allowing manufacturers to match consumer preferences.
- Noise Reduction: Molded components often feature properties that dampen sound, enhancing the overall driving experience.
Exterior Components
From bumpers to fenders, exterior components made from injected molds are critical for both safety and design.
- Impact Resistance: Injection-molded plastics provide essential protection while maintaining a lightweight profile.
- Weather Resistance: These components are designed to withstand harsh environmental conditions, ensuring reliability.
- Design Innovation: Molding techniques allow for unique shapes that improve aerodynamics and aesthetics.
Environmental Sustainability
As the automotive industry faces pressure to reduce its environmental footprint, automotive injection molding emerges as a sustainable solution.
- Recyclable Materials: Many of the plastics used in injection molding are recyclable, reducing landfill waste.
- Energy Efficiency: The injection molding process typically consumes less energy compared to other manufacturing methods.
- Life Cycle Assessment: Evaluating the overall environmental impact of injection-molded parts often reveals a smaller carbon footprint than alternatives.
Innovations in Automotive Injection Molding
The landscape of automotive injection molding is rapidly evolving. Recent technological advancements have revolutionized the way parts are produced.
3D Printing and Injection Molding Integration
The integration of 3D printing with injection molding processes allows for rapid prototyping and testing. Here are some benefits of this innovation:
- Faster Prototyping: Designers can quickly create models to test functionality before committing to expensive molds.
- Cost-Effective Changes: Minor design modifications can be easily implemented, saving time and resources.
- Complex Shapes: 3D printing enables the creation of complex shapes that would be difficult to achieve with traditional molding techniques.
Advanced Materials
New materials are continually being developed to improve the performance of injection-molded automotive components. Some noteworthy advancements include:
- Bio-based Plastics: These materials are derived from renewable sources, reducing dependency on fossil fuels.
- Reinforced Composites: Materials combined with glass or carbon fibers provide enhanced strength without adding significant weight.
- Smart Materials: Technologies that respond to environmental changes enhance the functionality of molded parts.
Challenges Facing the Automotive Injection Molding Industry
Despite its numerous advantages, the automotive injection molding sector is not without its challenges. Understanding these hurdles is essential for continuous improvement:
- High Initial Costs: The costs associated with creating molds can be a barrier for small manufacturers.
- Skill Shortages: The need for skilled labor is critical, and shortages can hinder production capabilities.
- Regulatory Compliance: Manufacturers must navigate complex regulations regarding materials and processes.
Future Trends in Automotive Injection Molding
Looking ahead, the future of automotive injection molding appears promising, with several trends expected to shape the industry:
Increased Automation
As manufacturers seek to boost efficiency and reduce operational costs, automation technologies such as robotics and AI will play an increasingly vital role in the injection molding process.
Focus on Lightweighting
With the automotive industry's ongoing commitment to fuel efficiency and emission reduction, lightweight materials will be prioritized in design and production.
Customization and Personalization
The rise of consumer demand for personalized vehicles will lead manufacturers to adopt more flexible injection molding processes to accommodate bespoke designs.
Conclusion
In conclusion, automotive injection molding is more than just a manufacturing process; it is a transformative force in the automotive industry. With its ability to deliver cost savings, design flexibility, and sustainability, it stands at the forefront of modern manufacturing. As technology continues to advance, the innovations within this field will undoubtedly propel the automotive industry into exciting new territories.
For businesses looking to leverage the advantages of automotive injection molding, partnering with experts like DeepMould.net can ensure success and competitive advantage in this fast-evolving market.