EPDM Rubber Testing: Ensuring Quality and Durability for Your Business
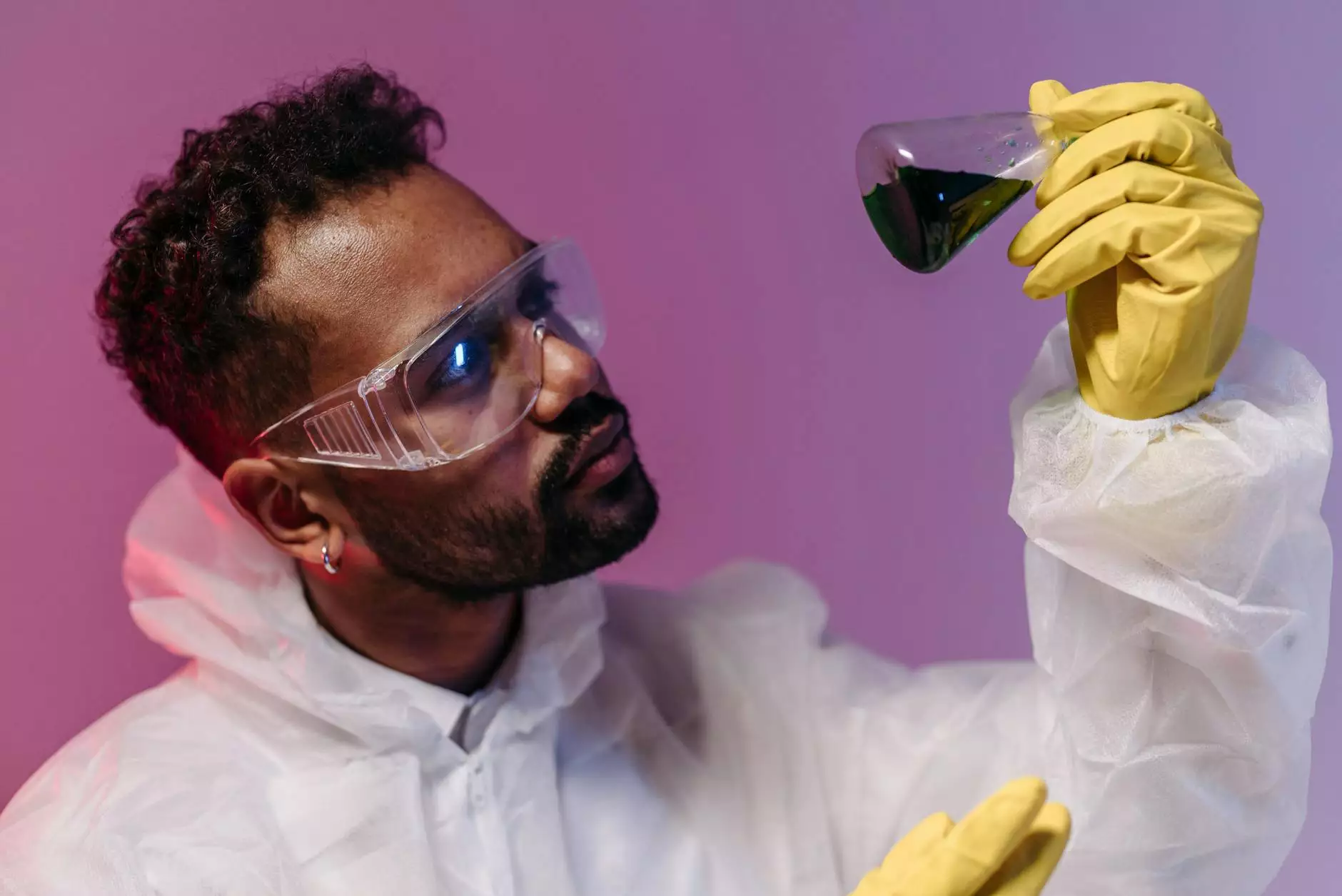
Understanding EPDM Rubber
EPDM rubber, or Ethylene Propylene Diene Monomer rubber, is a versatile synthetic rubber known for its excellent weather resistance, durability, and versatility. Used in various applications, from roofing membranes to automotive parts, EPDM’s unique composition allows it to perform well in extreme conditions, making it a favorite across multiple industries.
Why is EPDM Rubber Testing Essential?
In today’s competitive market, brands must prioritize quality to maintain customer satisfaction and compliance. EPDM rubber testing plays a crucial role in ensuring that the material meets specified standards for performance, reliability, and safety. The primary reasons for conducting EPDM rubber testing include:
- Quality Assurance: Testing guarantees that the rubber meets the quality standards necessary for the intended application.
- Regulatory Compliance: Many industries have specific regulations regarding materials used; testing ensures compliance.
- Consumer Safety: Ensuring the safety of products that utilize EPDM rubber is paramount.
- Durability and Longevity: Testing determines the longevity of EPDM rubber products, ensuring they can withstand environmental factors.
- Cost Efficiency: Proper testing can prevent costly recalls and ensure products meet performance expectations.
The EPDM Rubber Testing Process
The process of EPDM rubber testing typically involves several stages, each tailored to assess different properties of the rubber. Below, we outline the main stages in the testing process:
1. Material Composition Analysis
This initial step involves analyzing the rubber's chemical composition to ensure it adheres to industry standards. Techniques such as spectroscopy are often used to evaluate the material's formulation.
2. Physical Property Testing
Physical property testing measures various aspects of the EPDM rubber, including:
- Tensile Strength: Analyzes the maximum stress the material can withstand while being stretched.
- Elongation: Measures the rubber's ability to stretch before breaking.
- Hardness: Determines the rubber’s resistance to indentation, with a common gauge being the Shore durometer scale.
3. Environmental Resistance Testing
This testing phase evaluates how well the EPDM rubber performs under various environmental conditions, including:
- Ultraviolet (UV) Radiation: Assesses the rubber's resistance to fading and degradation from sun exposure.
- Ozone Resistance: Evaluates its performance against ozone and prevents cracking.
- Temperature Stability: Tests its ability to maintain performance in extreme hot or cold conditions.
4. Aging Tests
Aging tests simulate long-term usage conditions to predict the rubber's lifespan. These tests help determine how materials will degrade over time.
5. Fire Resistance Testing
For applications that involve potential fire hazards, conducting fire resistance testing is critical to ensure safety standards are met.
The Benefits of EPDM Rubber Testing for Your Business
Implementing a robust EPDM rubber testing protocol can yield numerous benefits for businesses, including:
- Enhanced Product Quality: Regular testing ensures that each batch of rubber maintains high quality and performance standards.
- Improved Customer Confidence: Clients are more likely to trust a brand that prioritizes material testing and quality assurance.
- Market Advantage: Offering products that are certified and tested can provide a competitive edge in the marketplace.
- Reduced Liability Risks: Comprehensive testing reduces the risk of product failures, which can lead to costly lawsuits or recalls.
Industry Applications of EPDM Rubber
EPDM rubber has a wide range of applications across various industries. Some common applications include:
- Construction: Used in roofing systems, waterproofing membranes, and seals.
- Automotive: Commonly found in weather stripping, hoses, and electrical insulation.
- Manufacturing: Employed in conveyor belts, seals, and gaskets due to its strength and durability.
- Electrical: Serving as insulation in electrical components thanks to its resistance to heat and electricity.
- Consumer Goods: Often found in household products like mats, pads, and toys.
Choosing the Right Testing Partner
When selecting a partner for EPDM rubber testing, several factors should be taken into consideration:
- Accreditation: Ensure the testing laboratory is accredited and follows ISO standards.
- Expertise: Look for companies with extensive experience in rubber testing.
- Advanced Technology: A laboratory that employs the latest testing technologies will provide the most reliable results.
- Reputation: Research customer reviews and case studies to gauge a company’s reliability.
- Custom Solutions: A good testing partner should be able to provide tailored testing solutions based on your specific requirements.
Conclusion: Elevating Your Business Standards
In conclusion, EPDM rubber testing is a crucial process that supports quality assurance, safety, and compliance across industries. By prioritizing rigorous testing protocols, businesses can enhance product quality, build customer trust, and ultimately secure a competitive edge in the market. As industries evolve and consumer expectations grow, maintaining high standards through comprehensive testing will set businesses apart. Don’t leave your product’s quality to chance—invest in reliable EPDM rubber testing today to ensure long-term success.
For more information about EPDM rubber testing and to explore our services, visit us at flexxerrubber.com.