Precision Moulding: A Cornerstone of Metal Fabrication
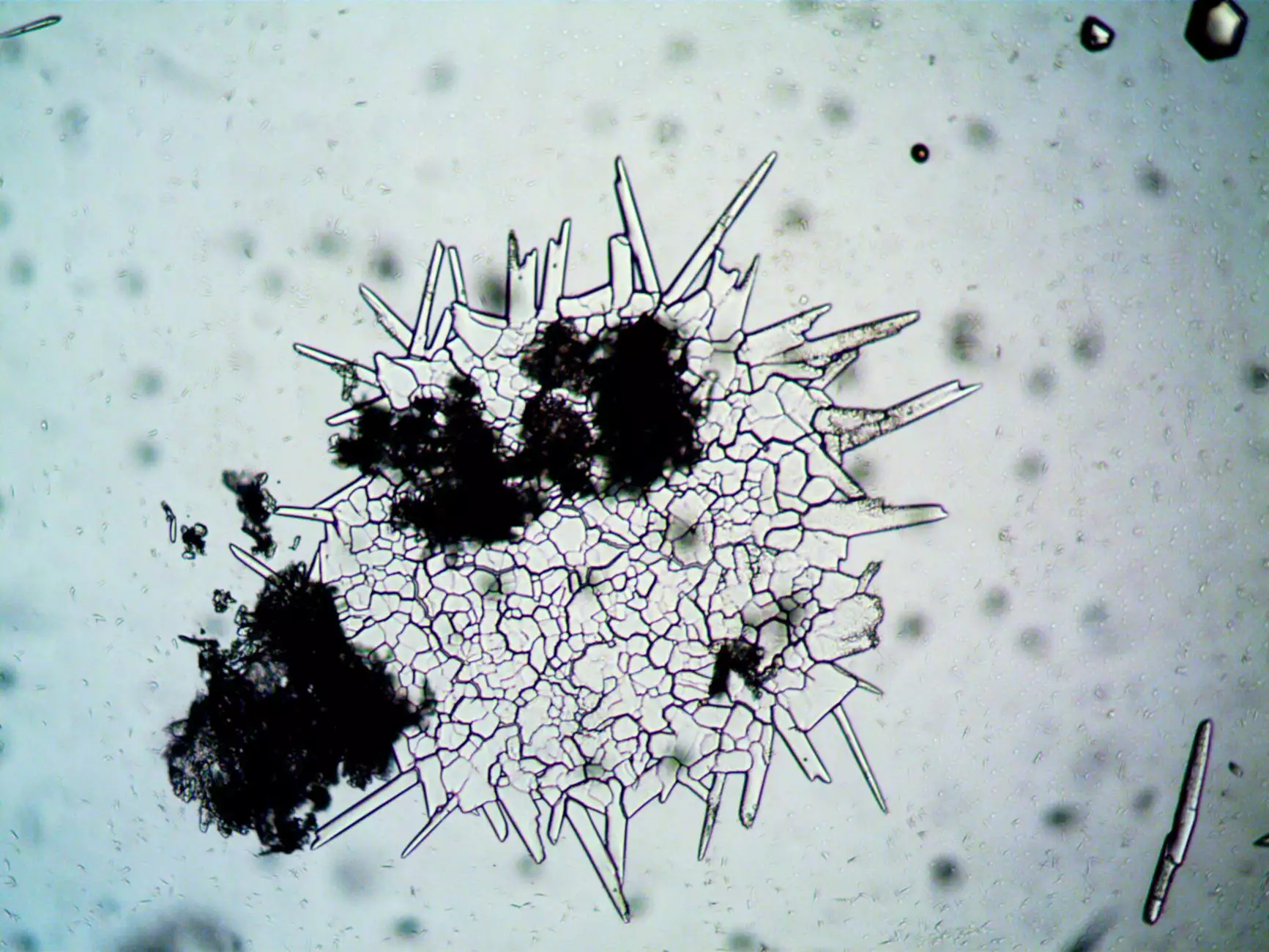
Precision moulding plays a pivotal role in the metal fabrication industry, serving as a fundamental technique that drives efficiency, accuracy, and quality in various manufacturing processes. As demand for intricate designs and durable products rises, understanding the intricacies of this process becomes essential for businesses, engineers, and manufacturers. This article delves deep into the world of precision moulding, examining its techniques, benefits, applications, and the future it promises for the industry.
The Fundamentals of Precision Moulding
Precision moulding refers to the process of creating precision-crafted components by shaping materials into specific forms through the use of molds. The process can involve various materials, although metals are the predominant choice in many industrial applications. This manufacturing technique allows for the production of complex designs with high levels of detail and repeatability.
Key Characteristics of Precision Moulding
- Accuracy: Achieving tight tolerances is one of the defining features of precision moulding.
- Efficiency: The ability to produce high volumes of identical parts rapidly, significantly reducing lead times.
- Material Versatility: While metals are common, the process can also accommodate various polymers and composites.
- Surface Finish: Precision moulding often results in superior surface finishes that require minimal post-processing.
The Process of Precision Moulding
The precision moulding process typically involves several key steps to ensure that the final product meets the quality standards required by industries such as automotive, aerospace, and electronics.
1. Design and CAD Modeling
The first step in the precision moulding process is the designing of the product. Engineers create detailed Computer-Aided Design (CAD) models, which provide the specifications and dimensions required for the mould.
2. Prototype Development
Before mass production begins, a prototype is often developed to assess the design's feasibility and functionality. This step can involve quick prototyping techniques such as 3D printing to test the form and fit.
3. Mould Fabrication
The mould itself must be crafted with great precision. Traditional methods use metals like steel or aluminum, which are machined to create the negative space required for the final product.
4. Mould Filling
Mould filling involves pouring or injecting the molten material into the mould cavity. The choice of filling method depends on the material properties and the product's design.
5. Cooling and Solidification
Once the mould is filled, the material is allowed to cool and solidify, taking the shape of the mould. The cooling time varies depending on the material used and the product's design.
6. Ejection and Finishing
After the material has cooled, the finished product is ejected from the mould. Depending on the application, some finishing processes, such as machining or coating, may be necessary to achieve the desired final properties.
Benefits of Precision Moulding
There are several advantages associated with employing precision moulding in metal fabrication:
1. Cost-Effectiveness
The ability to produce components in bulk with minimal waste makes precision moulding a cost-effective solution for manufacturers.
2. Enhanced Durability
Parts produced through precision moulding often exhibit superior mechanical properties compared to those created through less precise methods. This is crucial in applications requiring robust components.
3. Streamlined Production Times
Precision moulding significantly reduces production times due to its efficiency and high output rates, allowing businesses to meet deadlines and customer demands effectively.
4. High-Quality Aesthetics
The process yields components with exceptional surface finishes that require less additional work, enhancing the overall aesthetic appeal of the finished products.
Applications of Precision Moulding in Metal Fabrication
Metal fabrication leveraging precision moulding has an extensive range of applications across numerous industries:
1. Automotive Industry
In the automotive sector, precision moulding is utilized to manufacture a variety of components, including gear housings, brackets, and exterior trims, which require intricate shapes and durable materials.
2. Aerospace Engineering
The aerospace industry demands high-strength, lightweight components that can withstand extreme conditions. Precision moulding fulfills these requirements by allowing for the production of complex parts with high tolerances.
3. Electronics Manufacturing
In electronics, precision moulding is used to create casings, connectors, and other essential components that necessitate fine details and reliable performance.
4. Medical Devices
Precision moulding is a crucial process in producing components for medical devices, where precision and durability are critical for safety and efficacy.
The Future of Precision Moulding in Metal Fabrication
As technology advances, the future of precision moulding in metal fabrication looks promising. Several trends indicate an evolution in the processes and capabilities of precision moulding:
1. Integration of Advanced Technologies
Data analytics, AI, and IoT technologies are beginning to play a role in optimizing precision moulding processes. This could lead to even greater efficiencies and predictive maintenance of machinery.
2. Sustainable Practices
With a growing focus on sustainability, the industry is shifting towards using eco-friendly materials and processes in precision moulding. This involves developments in biodegradable materials and recycling technologies.
3. Customization and On-Demand Manufacturing
As customization becomes increasingly important to consumers, precision moulding will adapt to facilitate on-demand manufacturing, allowing businesses to produce tailor-made components without significant delays.
Conclusion
In conclusion, precision moulding stands as a key methodology within the metal fabrication sector, offering numerous benefits across various industries. As this process continues to evolve and integrate advanced technologies, businesses like deepmould.net can leverage it to provide superior products and maintain a competitive edge. Understanding and embracing the principles of precision moulding will undoubtedly shape the future of manufacturing, contributing to high-quality, cost-effective solutions that meet the demands of modern markets.