Understanding Air Compressor Inspection: Ensuring Your Business Operations Run Smoothly
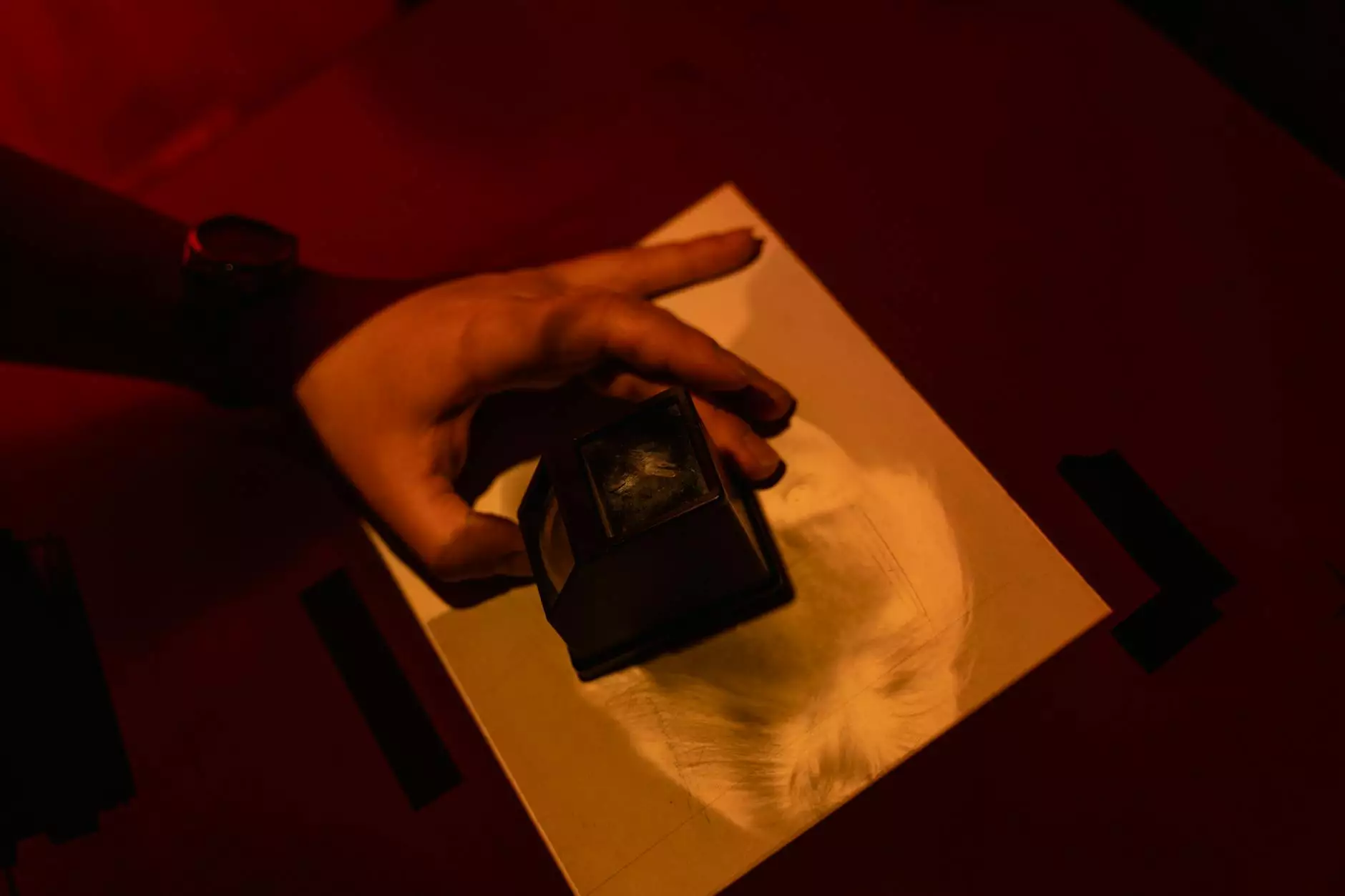
In the ever-evolving landscape of business, ensuring that your equipment is functioning optimally is paramount. One essential yet often overlooked aspect is the air compressor inspection. In industries ranging from manufacturing to gardening, maintaining the integrity of air compressors can significantly influence overall productivity and safety. This comprehensive guide will delve into the significance of air compressor inspections, the processes involved, and the benefits businesses like those in the Home & Garden, Gardeners, and Pest Control sectors can reap from regular maintenance.
Why Air Compressor Inspection is Vital for Your Business
Air compressors are the backbone of many operations. They provide energy for various tools and processes. Thus, conducting regular inspections is not merely a recommendation but a crucial requirement. Here's why:
- Enhances Safety: An inspected and well-maintained compressor reduces the risk of accidents caused by equipment failure.
- Improves Efficiency: Regular inspections help identify potential issues before they escalate, ensuring your equipment operates at peak performance.
- Extends Equipment Life: Routine maintenance significantly enhances the longevity of your air compressor, saving money on replacement costs.
- Ensures Compliance: Many industries have strict regulations regarding equipment maintenance. Regular inspections help you stay compliant.
- Environmental Impact: Well-maintained compressors operate more efficiently and can help reduce indoor air pollution, benefiting your workspace.
The Process of Air Compressor Inspection
The thorough inspection of an air compressor typically involves several key processes. Understanding these can empower your business to implement effective maintenance strategies.
1. Visual Inspection
A visual inspection is often the first step. Inspectors look for:
- Leaks in hoses and fittings
- Corrosion or signs of wear
- Obstructions around the compressor
- Proper ventilation and placement
2. Operational Checks
Next, the inspector will run the compressor to observe:
- Noise levels: Unusual sounds may indicate internal problems.
- Vibration: Excessive vibration can mean unbalanced components.
- Pressure levels: These should be consistent with manufacturer specifications.
3. Fluid Analysis
The inspection will usually include a review of the fluids used in the compressor:
- Oil analysis for contamination and viscosity
- Draining of moisture and sludge from the air receiver
4. Component Inspection
Inspecting the critical components of the air compressor is essential:
- Air filters need to be clean and unobstructed for proper air flow.
- Belts and hoses should show no signs of wear or fatigue.
- Valves and drains must function correctly to prevent pressure build-up.
5. System Testing and Documentation
Following the physical inspection, documentation is vital for tracking the compressor's health. Testing results should be documented to ensure:
- Compliance with industry standards
- A comprehensive log of maintenance performed
- Tracking trends over time to catch emerging issues early
Benefits of Regular Air Compressor Inspections
Investing time and resources into regular air compressor inspections can yield significant returns. Let's dive into some key benefits:
Cost Savings
While there is a cost associated with inspections, the savings from reduced downtime and more efficient operation often outweigh these costs. Businesses can save on:
- Repair costs due to early detection of issues
- Energy bills because well-maintained compressors consume less power
- Replacement costs as prolonged life means less frequent purchases
Operational Reliability
Reliable equipment is essential for maintaining the flow of business. Regular inspections help ensure:
- Uninterrupted operations that contribute to productivity
- Improved customer satisfaction through timely service delivery
Enhanced Employee Safety
When workers operate in an environment where the machinery is routinely inspected, the risks associated with equipment failure are dramatically reduced. Key aspects include:
- A decrease in workplace accidents related to machinery
- A safer work environment, promoting employee morale and productivity
Creating an Effective Inspection Program
To maximize the advantages of air compressor inspections, businesses need a structured inspection program. Here’s how to create one:
1. Schedule Regular Inspections
Depending on your compressor's usage and environment, determine the inspection frequency. For high-use compressors, monthly inspections may be necessary, while others may suffice with quarterly checks.
2. Train Your Staff
Ensure that your team understands the importance of these inspections. Training should include:
- Basic operational knowledge of the air compressor
- Recognizing signs that indicate problems
3. Partner with Professionals
If your team lacks expertise in conducting thorough inspections, partnering with a professional service, such as SafePlant UK, can be invaluable. Professionals can bring specialized knowledge and the necessary tools to conduct thorough inspections.
4. Keep Detailed Records
Maintain a detailed log of all inspections performed, including:
- Findings and actions taken
- Dates and personnel involved in inspections
- Trends or issues that require ongoing monitoring
Conclusion: The Path Forward with Air Compressor Inspection
In conclusion, ensuring that your air compressor undergoes regular inspections is not just a safety measure; it is a crucial component for maintaining operational efficiency and reliability. Businesses operating in varied sectors, including Home & Garden, Gardeners, and Pest Control, can significantly benefit from prioritizing regular maintenance. By understanding the inspection process, recognizing its importance, and creating a robust inspection program, you can safeguard your operations against potential pitfalls and set your business up for long-term success.
Embrace the culture of preventive maintenance within your organization and witness the transformation in productivity, safety, and cost savings. Remember, regular air compressor inspections are an investment in your business's future.